What are Gas Cooling Towers?
In the cement industry, a Gas Cooling Tower (GCT) plays a crucial role in conditioning the high-temperature exhaust gases generated during clinker production and other processes. The main objectives of a GCT are to reduce gas temperatures to optimal levels for dust collection, protect downstream equipment such as bag filters or electrostatic precipitators, and enhance the overall efficiency of the process.
Key Design Parameters:
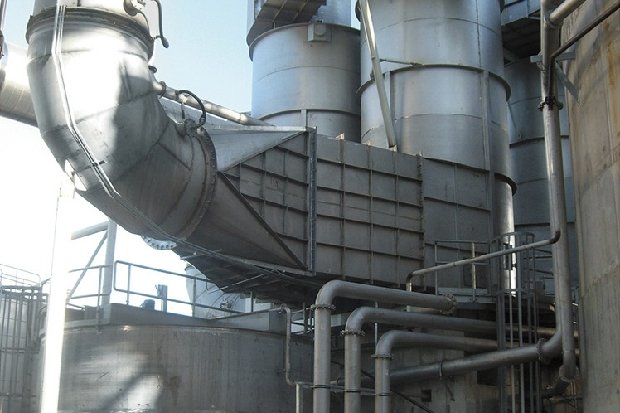
* Gas Inlet Temperature: The initial temperature of the exhaust gas, often exceeding 1,000°C, dictates the cooling capacity required.
* Gas Flow Rate: The volume of gas passing through the tower, typically measured in cubic meters per second (m³/s), affects the tower’s size and spray system design.
* Cooling Range: The desired reduction in gas temperature, usually to around 150°C–250°C, depending on process requirements and equipment tolerances.
* Water Injection System:
* Type: High-pressure nozzles or atomizers ensure fine droplet formation for effective cooling.
* Flow Rate: The water volume injected, calculated based on gas temperature, humidity, and cooling efficiency.
* Residence Time: The time gas spends in the cooling chamber, ensuring sufficient heat exchange and uniform temperature distribution.
* Material Selection: Corrosion-resistant materials, such as stainless steel, are used to withstand high temperatures and acidic gases.
* Evaporation Efficiency: Maximizing the cooling effect through controlled evaporation without over-saturating the gas.
* Dust Handling: The design must prevent water droplet condensation that can lead to clogging or mud formation in downstream equipment.